Design for Additive Manufacturing: Unleashing New Potentials in Business
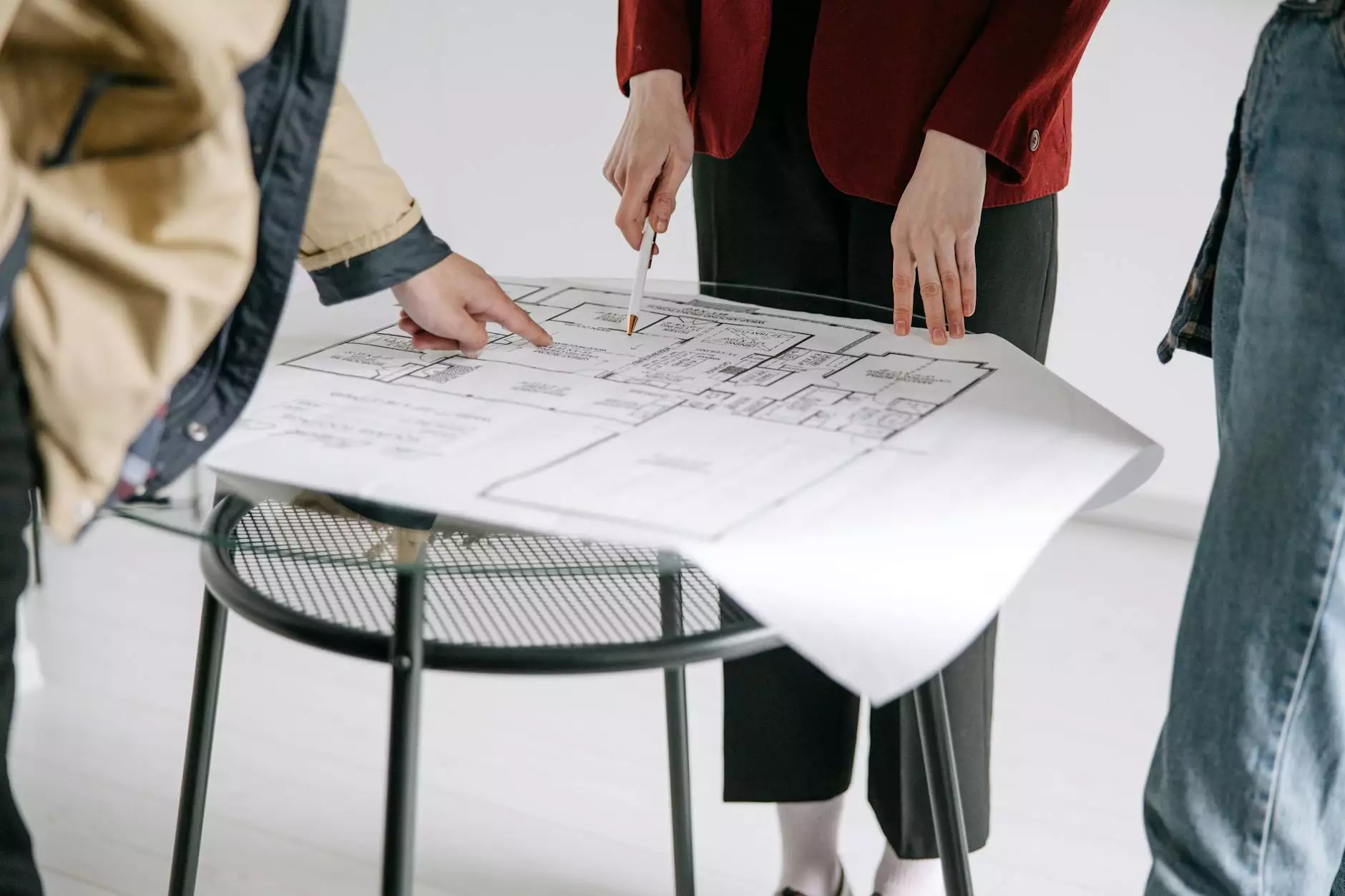
In today’s rapidly evolving industrial landscape, design for additive manufacturing (DfAM) signifies a pivotal shift in how products are conceived, created, and delivered. This approach not only reshapes traditional manufacturing paradigms but also introduces a myriad of opportunities for businesses in diverse fields, particularly in art supplies, product design, and 3D printing.
Understanding Additive Manufacturing
At its core, additive manufacturing encompasses a range of technologies that build products layer by layer, contrasting sharply with traditional subtractive manufacturing techniques. This innovative process allows for the creation of complex geometries that were previously unattainable. The implications for businesses are profound, offering increased design freedom, reduced material waste, and accelerated production times.
The Significance of DfAM in Business
The integration of design for additive manufacturing into business strategy delivers significant advantages:
- Enhanced Product Customization: Businesses can cater to unique customer needs by creating bespoke products that traditional manufacturing methods struggle to produce efficiently.
- Streamlined Supply Chains: DfAM enables on-demand production, minimizing the need for extensive inventories and reducing logistics costs.
- Fostering Innovation: The design freedom provided by additive manufacturing encourages companies to explore unconventional designs that inspire innovation.
The Role of DfAM in Art Supplies
The art supplies sector has witnessed a renaissance thanks to advancements in DfAM. Artists and designers can now produce tools and materials that were impossible to create through traditional means. Consider the following:
Creating Unique Tools and Mediums
With DfAM, artisans can design customized brushes, sculpting tools, and other artistic implements tailored to their specific techniques. For example, a sculptor can create a tool that mimics the texture of their preferred medium, enhancing their artistic process.
Personalized Art Supplies
Imagine a world where every artist can own tools that perfectly fit their hands and style. Through the customization capabilities of additive manufacturing, artists can now create ergonomic brushes or palette knives that enhance comfort and improve their craft.
Advancements in Product Design through DfAM
In the realm of product design, the impact of DfAM cannot be overstated. Designers are armed with extraordinary tools that allow them to challenge the status quo:
Rapid Prototyping
DfAM facilitates rapid prototyping, which enables designers to create, test, and refine their concepts in real time. This iterative process not only reduces time to market but also ensures products are optimized before full-scale production.
Complex Geometries for Functional Design
One of the most exciting aspects of DfAM is its ability to produce intricate designs that are both aesthetic and functional. For instance, lightweight lattice structures can be integrated into product designs, significantly reducing weight without sacrificing strength.
3D Printing: The Twin of Additive Manufacturing
3D printing is often used interchangeably with additive manufacturing, but it's essential to understand their relationship. While all 3D printing techniques fall under the umbrella of additive manufacturing, not all additive manufacturing is executed through 3D printing technologies.
Current advancements in 3D printing technologies, such as selective laser sintering (SLS) and stereolithography (SLA), have expanded the horizons for product design and creativity in ways previously thought impossible. Here are some key advancements:
- Material Diversity: New printable materials—from metals to bio-materials—allow designers to explore uncharted territories in both form and function.
- Enhanced Accuracy: Modern 3D printers offer higher precision, enabling intricate designs that closely align with the artist's vision.
- Eco-friendly Practices: Many 3D printing processes utilize less waste, contributing to more sustainable manufacturing practices.
Challenges in DfAM and the Way Forward
While the benefits of design for additive manufacturing are clear, businesses must navigate several challenges to fully capitalize on its potential:
Material Limitations
The diversity of materials in additive manufacturing is evolving, but challenges remain in terms of material properties, strength, and longevity. Businesses need to invest in research to identify materials that meet their specific requirements.
Skill Gaps
Transitioning to DfAM requires a skill set that may not be prevalent within traditional manufacturing companies. Upskilling the workforce and investing in training programs are essential strategies for businesses looking to adopt these technologies effectively.
The Future of Business with DfAM
The future of business, particularly in the fields of art supplies, product design, and 3D printing, relies heavily on successfully integrating design for additive manufacturing into everyday practices. Companies that prioritize innovation, sustainability, and customer-centric designs will likely thrive in this new landscape.
Conclusion
In conclusion, design for additive manufacturing represents a transformative force across various industries. By embracing its principles, businesses can unlock pathways to innovation, efficiency, and bespoke creations. As the technology of additive manufacturing continues to advance, the possibilities for artists, designers, and manufacturers will only enhance, creating a vibrant and dynamic marketplace that caters to the needs of the modern world.
For those ready to embark on this transformative journey, exploring resources, attending workshops, and leveraging platforms like arti90.com can provide essential insights and tools to stay at the forefront of this revolution.