Exploring the Potential of DED in 3D Printing
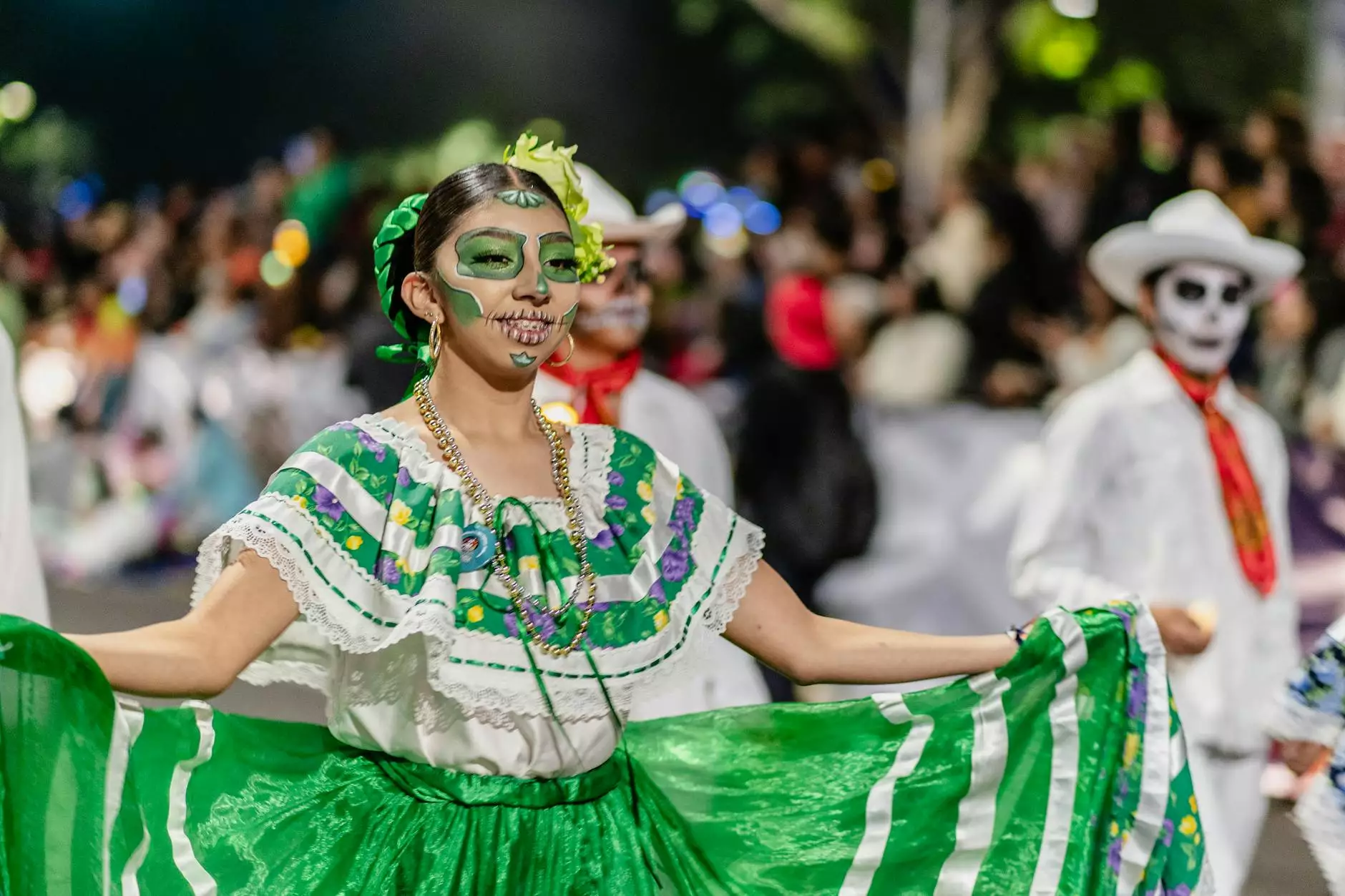
3D printing has transformed various sectors, offering innovative solutions to complex manufacturing challenges. Among the many techniques used in 3D printing, Directed Energy Deposition (DED) stands out due to its unique capabilities and applications. This article delves into the intricacies of DED, its benefits, applications, and the future prospects it holds in the realm of 3D printing.
What is DED?
Directed Energy Deposition (DED) is a 3D printing process that focuses on melting materials as they are deposited. This method uses a focused energy source, such as a laser, electron beam, or plasma arc, to create a molten pool of material onto a substrate or existing part. The primary materials used in DED are metal powders and wire, allowing for deposits that can build up and repair parts or produce new components.
How DED Works
The DED process involves several key stages:
- Preparation: The first step includes preparing the 3D model, which is typically designed using computer-aided design (CAD) software. The model must be sliced into layers suitable for the DED process.
- Material Feeding: In DED, either metal powder or wire is fed into the energy source’s melt pool. The choice of material is critical for the intended application.
- Energy Deposition: A concentrated energy beam melts the material. The molten material is then deposited layer by layer on a substrate.
- Cooling: As layers are deposited and built up, they cool and solidify to form a solid structure. This process can be controlled to achieve desired mechanical properties.
The Advantages of DED in 3D Printing
DED technology offers numerous advantages which make it a game-changer in the 3D printing world:
- Material Efficiency: DED allows for precise control of material usage, minimizing waste. This is crucial in industries where material costs are significant.
- Repair Capabilities: One of DED’s standout features is its ability to repair existing components. This capability extends the life of machinery and reduces costs associated with new parts.
- Versatility: DED is compatible with various materials, predominantly metals, making it suitable for multiple applications across industries such as aerospace, automotive, and medical devices.
- High Build Rates: DED's efficiency in depositing material allows for faster production times, particularly beneficial in industrial applications where time is crucial.
- Complex Geometries: Thanks to its layer-by-layer approach, DED can create highly intricate designs that may be challenging or impossible to achieve with traditional manufacturing methods.
Applications of DED Technology
With its impressive capabilities, DED finds applications across a variety of fields:
Aerospace
The aerospace industry utilizes DED for producing lightweight components that meet stringent performance standards. The ability to repair critical parts reduces downtime and costs associated with replacements.
Automotive
In automotive manufacturing, DED allows for rapid prototyping and the creation of customized components that enhance vehicle performance and design. The technology can also be used for repairing damaged parts, an aspect highly valued by manufacturers.
Medical
In the medical field, DED is employed to create patient-specific implants and prosthetics. The ability to produce complex geometries tailored to individual patients can significantly improve treatment outcomes.
Industrial Machinery
DED plays a vital role in the maintenance and repair of industrial machinery. Companies can quickly restore worn components, thus minimizing operational downtime—a critical factor in manufacturing environments.
Future Trends in DED Technology
The evolution of DED technology is expected to shape the future of manufacturing significantly:
- Integration with AI: The incorporation of artificial intelligence in DED processes can optimize parameter selection, improving print quality and efficiency.
- Hybrid Manufacturing: Combining DED with other manufacturing processes can create more robust and versatile production methods, allowing for greater design freedom and material properties.
- Sustainability: As industries move towards sustainable practices, the efficient use of materials offered by DED can contribute to greener manufacturing processes.
Challenges Facing DED Technology
Despite its numerous advantages, DED technology faces some challenges, including:
- Process Control: Ensuring consistent quality can be complex due to the variables involved in the deposition process, necessitating advancements in monitoring technologies.
- Material Limitations: While DED supports a variety of metal materials, the choice is still more limited compared to traditional forging or casting techniques.
- Technical Expertise: High levels of technical expertise are required to operate DED equipment effectively, which may pose a barrier for some manufacturers.
Conclusion
Directed Energy Deposition (DED) is revolutionizing the 3D printing industry by offering an innovative approach to manufacturing and repair. Its flexibility and efficiency make it an invaluable tool across various industries. As technology continues to evolve, the potential applications of DED will undoubtedly expand, leading to more advanced solutions and sustainable manufacturing practices. For those interested in staying ahead in the rapidly changing landscape of manufacturing, understanding and adopting DED technology is essential.
For more detailed information about DED and its applications, you can visit infotron.com.tr.