Unlocking the Potential of China Molds: A Deep Dive into the Future of Manufacturing
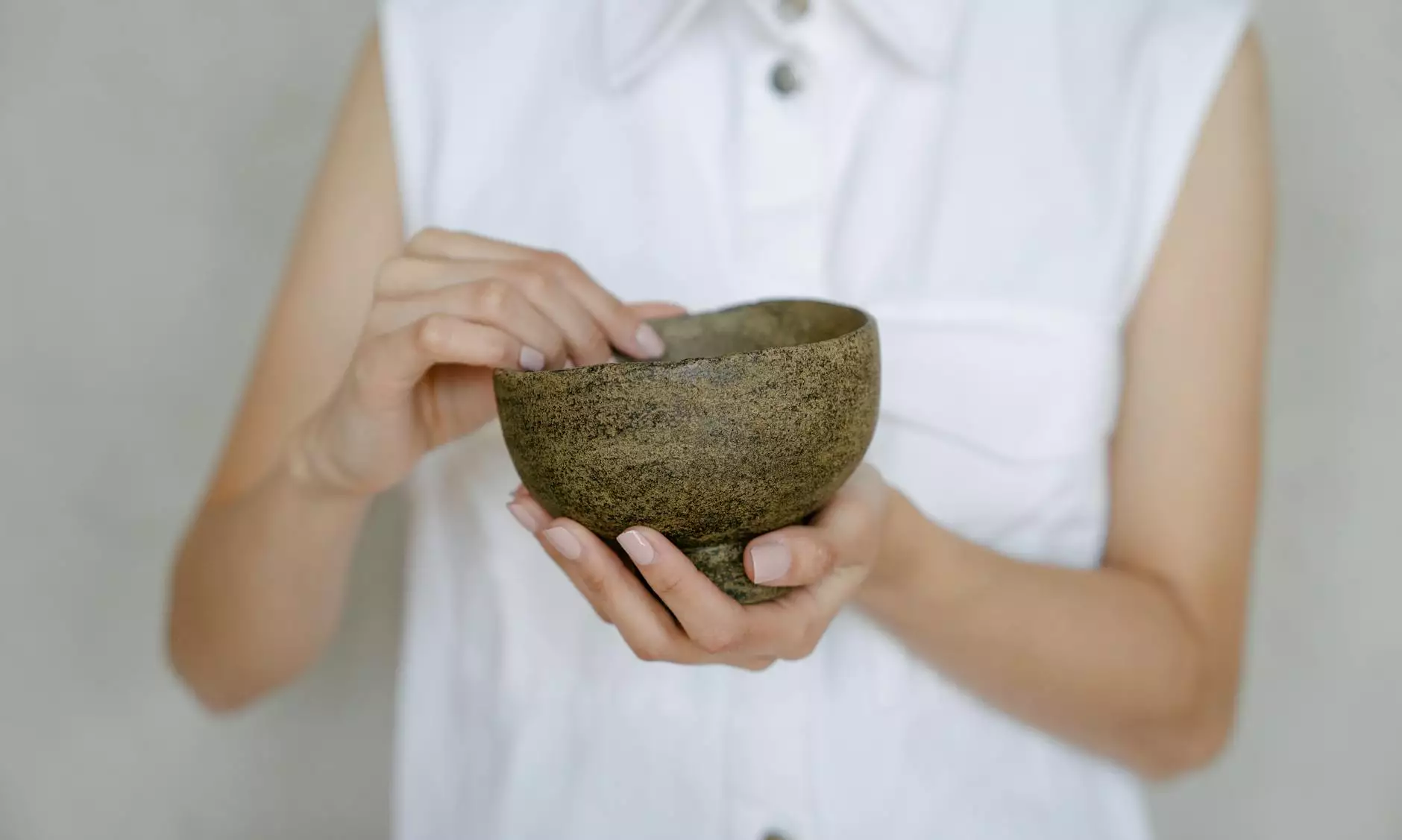
The global manufacturing landscape is evolving, and at the forefront of this revolution are the innovative processes associated with China molds. Known for their efficiency and precision, these molds not only redefine production standards but also provide a plethora of options for various industries. In this article, we will explore the intricacies of plastic mold making and plastic injection mould manufacturing offered by Hanking Mould, shedding light on how these elements serve as the backbone of modern manufacturing.
The Significance of China Molds in Contemporary Manufacturing
As the backbone of the production process, China molds play a critical role across multiple sectors including automotive, electronics, consumer goods, and medical devices. Their importance can be attributed to several factors:
- Cost-Effectiveness: The cost of labor and materials in China has enabled manufacturers to produce molds at a lower price, giving companies access to affordable yet high-quality products.
- Advanced Technology: Chinese manufacturers have increasingly integrated advanced technologies such as CNC machining and 3D printing into their mold-making processes, ensuring precision and quality.
- Custom Solutions: With a vast array of manufacturers, companies can find custom solutions tailored to their specific needs, ensuring that every mold meets the uniform standards of production.
- Rapid Turnaround: The streamlined processes and efficiencies developed in China allow for quicker turnaround times, which is essential in today’s fast-paced market.
Understanding Plastic Mold Making
Plastic mold making is an art as much as it is a science. The process involves several meticulous steps that ensure the final product meets all desired specifications. The stages of plastic mold making can be broadly categorized as follows:
1. Designing the Mold
The initial phase of mold production involves designing a mold that will produce the desired plastic parts. This step incorporates CAD (Computer-Aided Design) software to create detailed molds that reflect the specifications outlined by the client. Designers must consider:
- Product Complexity
- Material Selection
- Volume of Production
- Cost Constraints
2. Material Selection
Choosing the right materials for mold production is crucial. Common materials used include:
- Steel: Known for its durability, steel molds are ideal for high-volume production.
- Aluminum: Lightweight and cost-effective, aluminum molds are often used for low to medium volume runs.
3. Production of the Mold
This stage involves using various machining techniques to create the mold structure. Techniques such as:
- CNC Machining
- EDM (Electrical Discharge Machining)
- 3D Printing
are employed to achieve high precision in the mold cavities.
4. Testing the Mold
After molds are made, they undergo rigorous testing. This step is vital in ensuring that the mold performs well under production conditions. Testing can identify potential issues such as:
- Air Traps
- Cooling Channel Blockages
- Dimensional Accuracy
5. Final Adjustments
Based on the testing feedback, necessary adjustments are made to further enhance mold performance and product quality.
The Process of Plastic Injection Mould Manufacturing
Plastic injection mould manufacturing is a method that allows molten plastic to be injected into a mold to create robust and intricate plastic parts. Here’s how the process typically unfolds:
1. Melting the Plastic
Plastic pellets are heated until they melt, becoming a viscous material suitable for injection.
2. Injection into the Mold
The molten plastic is injected into the mold cavity under high pressure. This ensures that the material fills every part of the mold, capturing intricate details.
3. Cooling Period
Once injected, the plastic is allowed to cool and solidify. Cooling time varies based on the material and the thickness of the parts produced.
4. Ejection of the Finished Product
After the plastic has cooled sufficiently, ejector pins push the finished product out of the mold, making it ready for inspection and packaging.
Why Choose China Molds?
Choosing China molds from a reputable manufacturer such as Hanking Mould offers numerous advantages. Here are a few reasons why businesses should consider them:
- High-Quality Standards: Chinese manufacturers are increasingly adhering to international quality standards, ensuring products that are reliable and durable.
- Expertise and Experience: The vast experience in different industries equips manufacturers with the knowledge needed to produce molds that meet specific requirements effectively.
- Sustainability Practices: Many Chinese manufacturers are incorporating eco-friendly practices in their mold manufacturing processes, addressing the growing demand for sustainability in production.
Future Trends in China Molds
The landscape of plastic mold making and plastic injection mould manufacturing is constantly evolving. Some key trends to watch include:
1. Automation and Robotics
In the pursuit of efficiency and precision, more manufacturers are integrating automation and robotics into their mold-making processes. This shift not only speeds up production but also reduces errors associated with manual operations.
2. Industry 4.0 Integration
The rise of Industry 4.0 brings a new level of connectivity and data sharing across the manufacturing supply chain. China molds will increasingly leverage IoT and big data analytics to optimize manufacturing processes.
3. Customization and Personalization
As consumer demand shifts towards personalized products, mold manufacturers will need to adapt by creating highly customizable solutions that meet individual client needs.
4. Sustainable Manufacturing Practices
Environmental considerations are driving changes in the manufacturing sector. Expect to see greater adoption of sustainable practices, including recyclable materials and energy-efficient production processes.
Conclusion
In conclusion, China molds represent a significant advancement in the production process, providing manufacturers with the tools required to succeed in a competitive market. With a focus on quality, efficiency, and innovation, companies such as Hanking Mould are set to lead the way in reshaping the future of manufacturing. By embracing the latest trends and technologies, businesses can ensure they remain at the cutting edge of their industries.
As global demand for high-quality molded products continues to rise, investing in China molds will be a pivotal decision for manufacturers looking to enhance their production capabilities and meet evolving consumer preferences.