Understanding the Importance of Automobile Plastic Mold in Modern Manufacturing
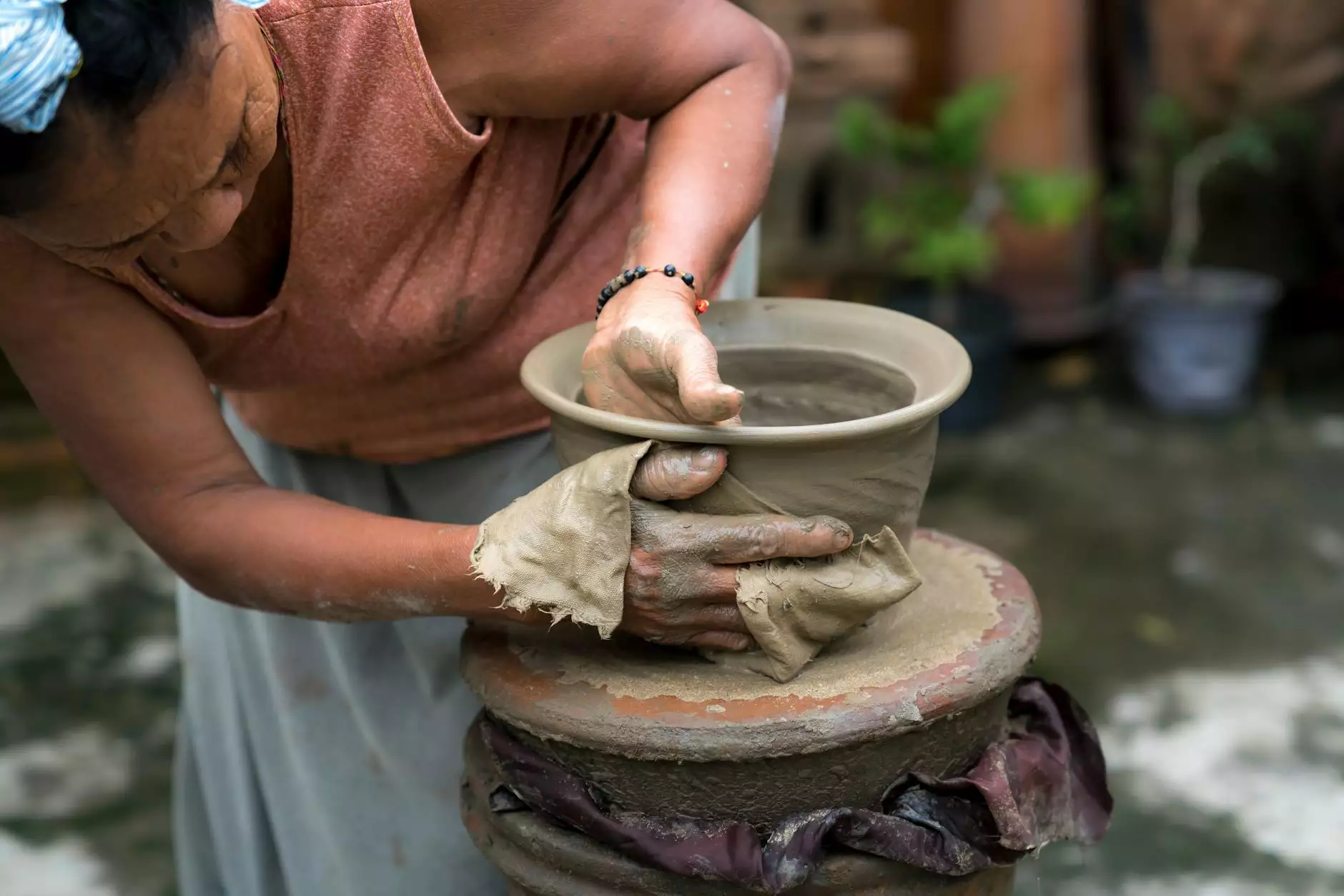
The manufacturing industry, particularly in the automotive sector, is rapidly evolving. One of the key components that facilitate this advancement is the automobile plastic mold. This article explores the integral role of automobile plastic molds in manufacturing, their benefits, and how businesses can leverage them for high-quality production.
The Evolution of Plastic Molding in Automotive Manufacturing
The journey of plastic molding in the automotive industry has been one of innovation and adaptation. Historically, automobiles were predominantly made from metal, but as technology progressed, manufacturers turned towards plastic for various reasons:
- Weight Reduction: Plastics are significantly lighter than metals, which contributes to improved fuel efficiency.
- Cost-Effectiveness: The production cost of plastic parts is generally lower than that of metal parts.
- Design Flexibility: Plastics allow for complex shapes that are often not feasible with metals.
- Corrosion Resistance: Plastics do not corrode, which increases the lifespan of components.
What is an Automobile Plastic Mold?
An automobile plastic mold is a manufacturing tool used to shape and convert plastic materials into specific automotive parts. The process involves injecting molten plastic into a mold where it cools and solidifies into the desired form. This method, known as injection molding, is widely praised for its efficiency and precision.
Types of Plastic Molds Used in Automobiles
Different types of molds are employed in the automotive industry:
- Injection Molds: The most common type, ideal for producing high volumes of identical parts.
- Blow Molds: Used for hollow plastic parts, such as fuel tanks.
- Thermoforming Molds: Utilized for shaping plastic sheets into automotive components.
- Compression Molds: Typically used for rubber and thermoset plastics.
The Advantages of Using Automobile Plastic Molds
Incorporating automobile plastic molds in the manufacturing process offers numerous advantages:
1. Enhanced Production Efficiency
Plastic molding allows manufacturers to produce parts quickly and in large quantities. The rapid cycle times of injection molding lead to increased productivity, enabling companies to meet high demand.
2. Precision Engineering
Automobile plastic molds provide exceptional dimensional accuracy. This precision is vital in achieving the intricate designs and specifications required in modern vehicles.
3. Versatility in Design
One of the standout features of plastic parts is their ability to be molded into complex shapes and designs. This flexibility gives automotive engineers and designers more freedom to innovate.
4. Lightweight Components
Reducing the weight of vehicles helps improve overall performance and fuel efficiency. By using plastic molds, manufacturers can create lighter components without sacrificing strength or durability.
5. Environmental Benefits
Plastic parts are often recyclable. Many manufacturers are now focusing on sustainable practices, utilizing recycled materials in their production processes, which contributes to a healthier planet.
Challenges in Automobile Plastic Molding
While there are many advantages, there are also challenges associated with automobile plastic molds:
1. Material Limitations
Not all plastics are suitable for every automotive application. Understanding the characteristics of various resin types is crucial for selecting the right materials for specific uses.
2. Initial Investment Costs
Creating molds, especially high-precision molds needed for the automobile industry, can require a significant upfront investment. However, this is often offset by long-term savings in production efficiency.
3. Quality Control Standards
Maintaining consistent quality across large production runs is essential. Implementing rigorous quality control measures is necessary to ensure that each component meets industry standards.
The Future of Automobile Plastic Molds
The future of the automobile plastic mold industry looks promising as technology advances. Innovations in material science, such as bio-based plastics and improved recycling processes, will enhance the sustainability and performance of automotive components.
Smart Manufacturing and Automation
With the rise of Industry 4.0, automobile manufacturers are adopting smart molding processes. Automation, artificial intelligence, and data analytics are beginning to play an essential role in optimizing production lines, improving quality control, and reducing waste.
Conclusion
In conclusion, the role of automobile plastic molds in the automotive industry cannot be understated. They offer numerous advantages, including increased efficiency, design versatility, and significant weight reduction. While challenges exist, the ongoing advancements in technology and materials will continue to push the boundaries of what is possible in automotive manufacturing.
As we look to the future, it is clear that plastic will remain a crucial component in the evolution of vehicle design and production. Businesses like DeepMould.net are at the forefront of this transformation, helping to shape a new era in automotive manufacturing through the innovative use of plastic molds.
© 2023 DeepMould.net. All rights reserved.