The Significance of Hydraulic Balls in Modern Industry
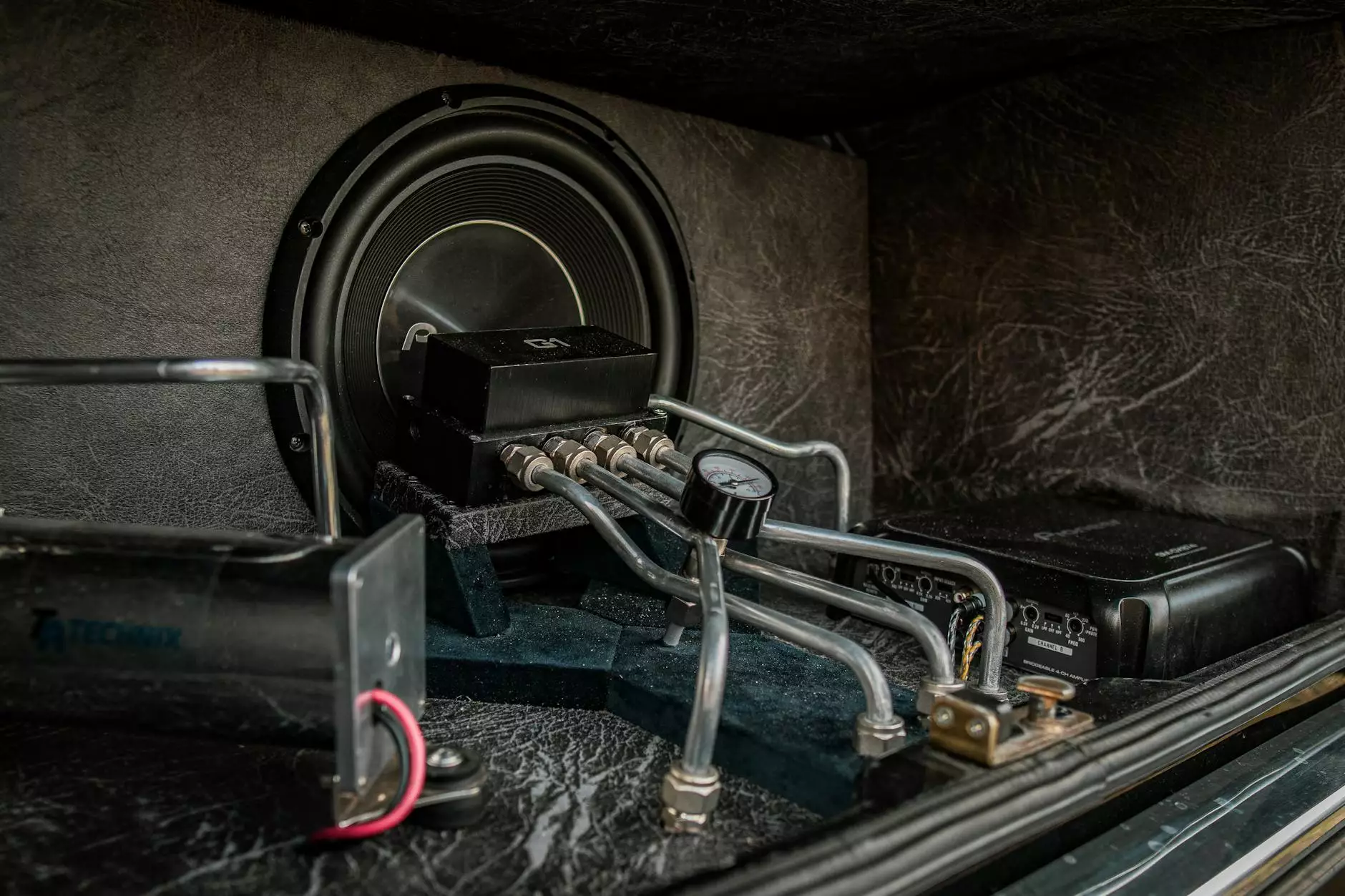
The world of industrial applications is defined by its reliance on effective fluid control systems. Among the myriad of components used, hydraulic balls stand out for their unique benefits and versatility. In this article, we explore the various aspects of hydraulic balls and their critical role in ensuring smooth operations across various industries. From their construction to applications and advantages, we aim to provide a comprehensive overview that demonstrates their importance in fluid dynamics.
What is a Hydraulic Ball?
A hydraulic ball is a type of valve or fitting that is used in various hydraulic systems to control the flow of fluids. These balls are typically made of durable materials such as stainless steel or brass, which offer excellent resistance to corrosion and wear. The design allows them to be perfectly spherical, ensuring a tight seal when closed. This is crucial for preventing leaks and maintaining optimal efficiency in hydraulic systems.
Understanding the Functionality of Hydraulic Balls
The primary function of a hydraulic ball is to manage the flow of hydraulic fluids. They operate on a straightforward principle: when rotated 90 degrees, they either allow or block the flow of fluid. This simple mechanism makes them integral to a variety of applications, including:
- Fluid Control - Managing the flow and pressure of fluids in hydraulic systems.
- Isolation - Providing a means to isolate portions of the system for maintenance or repairs.
- Diverting Flow - Changing the direction of fluid flow as needed within a hydraulic system.
Applications of Hydraulic Balls Across Industries
Hydraulic balls are utilized in many industries due to their essential role in fluid management. Here are some of the most common applications:
1. Manufacturing and Assembly Lines
In manufacturing processes, hydraulic systems are often employed to power machinery and conveyor belts. Hydraulic balls play a vital role in controlling the flow of hydraulic fluid that powers these systems, ensuring machinery operates smoothly and efficiently.
2. Automotive Industry
The automotive industry utilizes hydraulic balls in various applications, including brake systems and power steering. Their reliability and ability to withstand high pressures make them ideal components for ensuring safety and performance in vehicles.
3. Agriculture
In agriculture, hydraulic systems are widely used in equipment such as tractors and harvesters. Hydraulic balls are utilized to control the hydraulic flow necessary for operating different implements, enhancing overall productivity in farming operations.
4. Construction
Construction machinery, such as excavators and bulldozers, relies heavily on hydraulic systems for movement and operation. Hydraulic balls are key to regulating the fluid that powers these massive machines, ensuring they can perform under demanding conditions.
5. Oil and Gas Industry
In the oil and gas sector, hydraulic systems are crucial for drilling and extraction processes. Hydraulic balls help control the flow of fluids, minimizing the risk of leaks and ensuring operational safety in challenging environments.
The Advantages of Using Hydraulic Balls
Investing in high-quality hydraulic balls offers numerous advantages for industries reliant on hydraulic systems. Some of the key benefits include:
- Durability - Made from robust materials, hydraulic balls are designed to withstand extreme pressures and harsh environments.
- Efficiency - They provide a tight seal, minimizing fluid loss and enhancing the overall efficiency of hydraulic systems.
- Easy Maintenance - Hydraulic balls are typically easy to install and maintain, reducing downtime in industrial operations.
- Versatility - Available in various sizes and configurations, hydraulic balls can be adapted to a wide range of applications and systems.
Choosing the Right Hydraulic Ball for Your Application
When selecting a hydraulic ball for your system, several factors should be considered to ensure optimal performance. Here are some crucial elements to keep in mind:
1. Material Type
The material of the hydraulic ball is crucial in determining its durability and compatibility with different fluids. Common materials include:
- Stainless Steel - Recommended for high-corrosion environments.
- Brass - A cost-effective option for less demanding applications.
- Plastic - Suitable for lighter applications where weight is a concern.
2. Size and Pressure Rating
Ensure that the hydraulic ball you select has the appropriate size and pressure rating for your specific system requirements. This information is typically provided by the manufacturer and should align with your system’s specifications.
3. Seal Design
Different applications may require various seal designs to ensure compatibility with the fluids being used. Choosing a hydraulic ball with the right seal for your specific needs is crucial for preventing leaks and maintaining system integrity.
Hydraulic Ball Manufacturing Process
The manufacturing of hydraulic balls involves several key steps, ensuring that each component meets stringent quality standards. Here’s an overview of the process:
1. Material Selection
The first step in the manufacturing process is selecting the appropriate material based on the intended application and environmental conditions.
2. Machining
Once the material is selected, it is machined into the desired shape. Precision is key in this stage, as even slight inaccuracies can affect the performance of the hydraulic ball.
3. Heat Treatment
Heat treatment may be applied to enhance the durability and performance characteristics of the hydraulic ball, especially in high-pressure environments.
4. Surface Finishing
The surface is then finished to achieve the required smoothness, which is vital for the sealing capabilities of the hydraulic ball.
5. Quality Control
Finally, each hydraulic ball undergoes rigorous quality control tests to ensure it meets industry standards and customer expectations.
Innovative Trends in Hydraulic Ball Technology
As industries evolve, so do the technologies associated with hydraulic systems. Here are some innovative trends impacting the future of hydraulic balls:
1. Smart Hydraulic Systems
With the rise of Industry 4.0, smart hydraulic systems that integrate sensors and IoT capabilities are becoming more popular. These systems provide real-time data on performance, which is valuable for predictive maintenance and efficiency monitoring.
2. Eco-Friendly Materials
There is a growing trend towards the use of eco-friendly materials in hydraulic ball manufacturing, aimed at reducing environmental impact while maintaining performance standards.
3. Improved Design Features
Manufacturers are continuously working on improving design features that enhance the reliability and functionality of hydraulic balls, such as advanced seal technologies that further reduce leakage.
Conclusion
In conclusion, hydraulic balls are indispensable components within various hydraulic systems, serving critical functions across numerous industries. Their durability, efficiency, and versatility make them a popular choice for fluid control. By understanding the benefits and applications of hydraulic balls, industries can better optimize their operations, enhance safety, and increase productivity.
For those looking for high-quality fittings, including hydraulic balls, visit fitsch.cn. Investing in superior hydraulic components is essential for maintaining effective and reliable operations in today’s fast-paced industrial environments.